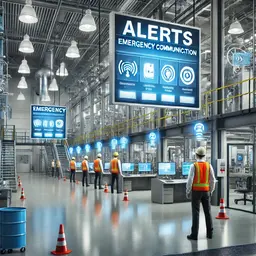
In the dynamic and fast-paced environment of manufacturing, safety and efficiency are paramount. With the complexities of managing large facilities, operating heavy machinery, and coordinating teams across various areas, the importance of an effective emergency communication system cannot be overstated. These systems serve as a lifeline in times of crisis, ensuring that employees are safe, operations are uninterrupted, and risks are mitigated. This article delves into why emergency communication systems are vital in the manufacturing industry and how they contribute to creating a safer and more efficient workplace.
Why Emergency Communication Systems Matter in Manufacturing
1. Rapid Response to Emergencies
Manufacturing facilities often involve high-risk environments, with the potential for accidents such as fires, chemical spills, equipment malfunctions, or natural disasters. An emergency communication system ensures that the right people are alerted immediately, enabling a swift response. Whether it’s evacuating employees, containing a fire, or addressing a machinery breakdown, quick communication can minimize damage and save lives.
2. Ensuring Employee Safety
In large manufacturing facilities, communicating effectively with employees across various departments and zones can be challenging. Emergency communication systems bridge this gap by delivering clear, instant messages to everyone, regardless of their location. Features such as intercom systems, mass text alerts, and loudspeakers help disseminate critical information, ensuring employees know exactly what to do during an emergency.
3. Maintaining Operational Continuity
Emergencies can disrupt manufacturing processes, leading to significant financial losses. A robust emergency communication system helps minimize downtime by providing real-time updates and instructions. For example, if a production line experiences a mechanical issue, the system can alert maintenance staff immediately, preventing the issue from escalating and keeping operations running smoothly.
4. Compliance with Safety Regulations
Regulatory bodies often mandate that manufacturing facilities have effective emergency communication systems in place. These systems are a critical component of occupational safety standards, such as those set by OSHA (Occupational Safety and Health Administration). Non-compliance can result in hefty fines or legal liabilities, making emergency communication systems a necessary investment.
Key Features of an Effective Emergency Communication System
Real-Time Alerts
The ability to send real-time alerts is crucial in manufacturing facilities, where even a few seconds can make a difference. Systems should support multiple communication channels, including text messages, emails, phone calls, and audible alarms.
Integration with Existing Systems
Modern emergency communication systems can integrate seamlessly with other safety systems, such as fire alarms, access control, and video surveillance. This integration ensures a cohesive response to emergencies, enabling better coordination.
Two-Way Communication
Two-way communication capabilities allow employees to report incidents or seek help during emergencies. This feature is especially useful for lone workers or employees in isolated areas of a facility.
Customizable Messaging
Manufacturing facilities have unique risks depending on their operations. A good emergency communication system allows for customizable messaging tailored to specific scenarios, such as chemical spills, equipment failures, or severe weather.
Scalability
As manufacturing facilities grow or expand, their emergency communication systems should be able to scale accordingly. Scalable systems ensure that all areas of a facility, regardless of size, are covered.
Examples of Emergency Communication Systems in Action
Case Study 1: Fire Emergency
A manufacturing plant producing automotive parts experienced a sudden fire in its storage area. The emergency communication system immediately activated fire alarms and sent evacuation instructions via intercom and text messages. Thanks to the system, all employees evacuated safely, and the fire was contained before causing significant damage.
Case Study 2: Chemical Spill
In a chemical manufacturing facility, a spill occurred due to a container rupture. The emergency communication system sent out alerts to employees in the affected area, directing them to evacuate while notifying the hazmat team. The quick response minimized exposure and ensured a safe cleanup process.
Case Study 3: Severe Weather
A metal fabrication plant faced an unexpected tornado warning. The emergency communication system alerted employees to take shelter in designated safe zones. The system also provided updates on weather conditions, ensuring everyone remained safe until the danger passed.
Benefits of Investing in Emergency Communication Systems
1. Enhanced Safety Culture
Emergency communication systems foster a culture of safety in manufacturing facilities. Employees feel more confident knowing that there are measures in place to protect them during crises.
2. Reduced Downtime
By enabling quick responses to emergencies, these systems help minimize operational disruptions and reduce downtime, saving companies significant costs.
3. Improved Risk Management
Proactive communication ensures that risks are managed effectively, reducing the likelihood of accidents and improving overall workplace safety.
4. Employee Morale and Retention
Employees are more likely to stay with companies that prioritize their safety. Emergency communication systems demonstrate a commitment to employee well-being, boosting morale and retention rates.
Choosing the Right Emergency Communication System
When selecting an emergency communication system for a manufacturing facility, it’s essential to consider the following:
- Ease of Use: Systems should be user-friendly to ensure quick activation during emergencies.
- Reliability: The system must function reliably even during power outages or network failures.
- Coverage: Ensure the system covers all areas of the facility, including outdoor spaces and remote zones.
- Regular Testing: Regular drills and testing ensure the system functions as intended and that employees are familiar with its use.
Conclusion
In the manufacturing industry, where safety and efficiency are critical, an effective emergency communication system is indispensable. These systems save lives, protect assets, and ensure business continuity during crises. By investing in modern, reliable communication tools, manufacturing facilities can create safer environments for employees and maintain smooth operations even in the face of emergencies.
Prioritize safety and operational efficiency in your manufacturing facility by implementing a robust emergency communication system. Don’t wait for an emergency to highlight the gaps—act now to safeguard your employees and operations.